by Dr. Anne Norcliffe
Dr. Anne Nortcliffe reflects on the affect that the COVID-19 pandemic and BREXIT has had on the UK’s economy, making the case to recognise where businesses have adapted to continue to be successful in such difficult circumstances.
Recognising Resilience in UK Businesses
The resilience displayed by UK businesses has enabled many to experience growth, realised through the professional approaches that have supported rapid adjustments in business models. Willingness to adopt agile ways of working has been key to continued business operations, through interventions and adjustments including:
- Staff working alternative shift patters and rotations,
- Safe social distancing in working situations,
- Remote secure working practices wherever possible,
Coupled with access to COVID-19 secure engineering and manufacturing facilities, these tactical changes in approach have all contributed to businesses being able to adapt to an external environment that would otherwise have been completely outside of their control.
Rapid Improvements in Hygiene Practices, Borrowed from Engineering Facilities
The first lockdown in March 2020 led to the urgent need for large-scale increases in the manufacture and distribution of PPE and hand sanitiser products. Existing UK manufacturing firms were able to meet this unprecedented increase in demand by flipping their business models and repurposing their manufacturing facilities to support the NHS and care homes and is one of many positive outcomes observed within the UK.
It is also important to understand how the hygiene practices used in modern engineering facilities aided other workplace adaptations to enable them to become ‘COVID-19 Secure’.
Many office spaces and retail outlets had an unpredicted new set of requirements that they met through investment, to address the vast increase in hygienic working practices as mandated by the UK Government. The aim was to help reduce the spread of COVID-19 while enabling businesses to continue to meet the new health and safety needs of their employees and customers. The success in making these environments ‘COVID secure’ was enabled, in part, due to the use of practices that were already commonplace in engineering industrial facilities for the last decade.
Engineering, as a industry today, is defined through total quality management practices. Lean and six sigma initiatives had already instigated hygienic sterile white and clean engineering manufacturing environments, more akin to surgical theatre than what many may see as being grey, industrial-style aesthetics.
Adopting such approaches has been shown to improve the health and safety of the employees, the engineering precision and quality of the products manufactured, reduce manufacturing time through reduced volume product re-work and additional finishing activities, while also leading to an increase in revenue streams from well managed waste separation processes.
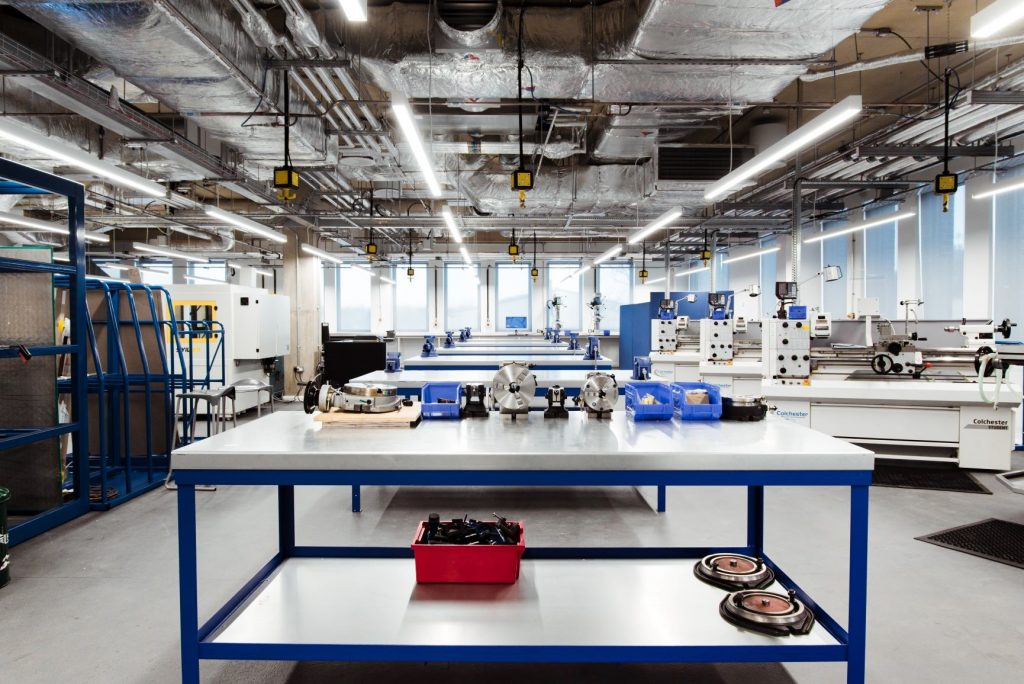
When combined, these improvements have enabled small-medium enterprises (SMEs) to adopt the same quality practices used in larger firms in an efficient way, enabling them to become approved tier suppliers to higher revenue and stricter quality controlled engineering industries, including aerospace and medical.
The willingness of UK manufacturing to be agile is testament to their ability to successfully react to the needs of the external operating environments through investment into industry 4.0 technologies, such as robotic feeders for automated CNC machine, the use of full industrial AI-led automation, and similar mechanisms in support of their business-to-manufacture value chain that can now operate for near-24/7 with minimum human intervention and product rework.
Advancement of automated feeding and manufacturing equipment also has the potential with secure digital communications to support remote working practices, including the configuration and monitoring of processes related to manufacturing operations.
With These Improvements Realised We Need to Look Forward
Within UK, many businesses therefore have successfully adapted, but there is still more to do. Freight prices have seen major increases due to the combined effects of COVID-19 and BREXIT. This is impacting on the cost savings of having goods manufactured in China and India, resulting in diminishing financial returns. This has already been evidenced this year through the volume of empty containers at UK ports, reaching unprecedented levels due to the high costs and limited return on shipping empty, or partially filled, containers back to Asia.
In addition, BREXIT is requiring European companies to register with the UK HMRC to ship goods to the UK. The ‘rules of origins’ are complicating UK industry business operations as any goods manufactured in the UK using source materials/parts from other countries require UK enterprises to apply different duties when selling into Europe.
Reducing freight and logistics costs, industries’ dependence on raw materials and parts from outside the UK are now all-important considerations for many enterprises’ supply-chains. They need to be reviewed to ensure their products continue to remain profitable and re-shoring manufacturing in the UK is now being invested in to reduce the reliance on long-haul freight, and reduce impact of BREXIT changes. Also the reliance on goods requiring long haul freight from overseas requires greater long-term planning and includes 3 to 6 month lead times, which does not support the previously mentioned business agility, in responding to data intelligence opportunities to pivot to enable businesses to continue to survive and grow onwards and out following the pandemic.
Reflections of Role of Data Intelligence
Zara’s business model, for example, have demonstrated success in this area as they had already previously moved production to be in-house. This enabled the fast-fashion business to rapidly respond to market data to increase stock in store of selling lines or adjust to changes in the global marketplace . Other businesses should look at their business model and supply chains to gain inspiration from their approach.
McDonalds is another good example, having learnt from the first lockdown where they cancelled all lettuce orders at the time. This meant that they could not re-open immediately after the first lockdown was lifted as it takes 45 days to grow lettuce. McDonalds now works closely with suppliers, experimenting with new lines, using strong data intelligence to identify potential successful new product lines through pilot trials in certain locations, while working with local suppliers to ensure they are viable.
The clear movement here is that businesses need to recoup losses in long-haul freight from Asia, while also putting in place models that support rapid adjustment and adaptations. Industry 4.0 technologies automation, data intelligence, and continuing to make use of lean and Six Sigma approaches will enable this to take place in a strategic way. The main aim of this is to reduce product waste while supporting cost effective and timely local, and national manufacturing solutions.
Taking Advantage of the Opportunities that are Still Available
With all this said, even in such a challenging environment, opportunities are still available for a number of business sectors that can be realised through inter-industry collaboration to provide local and national solutions that yield quality improvements, time efficiencies, and environmental and fiscally advantageous outcomes for UK businesses.
The streamlining of processes and collaboration for construction firms have already enabled off-site construction specialists to start building homes that are ready to live in, in just eight weeks, compared to six months to a year for a traditional build. The key is through the use of in-shore Industry 4.0 manufacturing solutions that can provide agility and resilience, feeding back into the economy through growth of business activity.
Collaborating through CCCU
If anything in this article has been of interest to you and you are working in an industry that could benefit through accessing the University’s collaborative networks, or are thinking about upskilling your staff base, or retraining yourself, contact edgehub@canterbury.ac.uk to arrange a business discussion on what the University can do to help your business or personal career aspirations as a response to the pandemic.